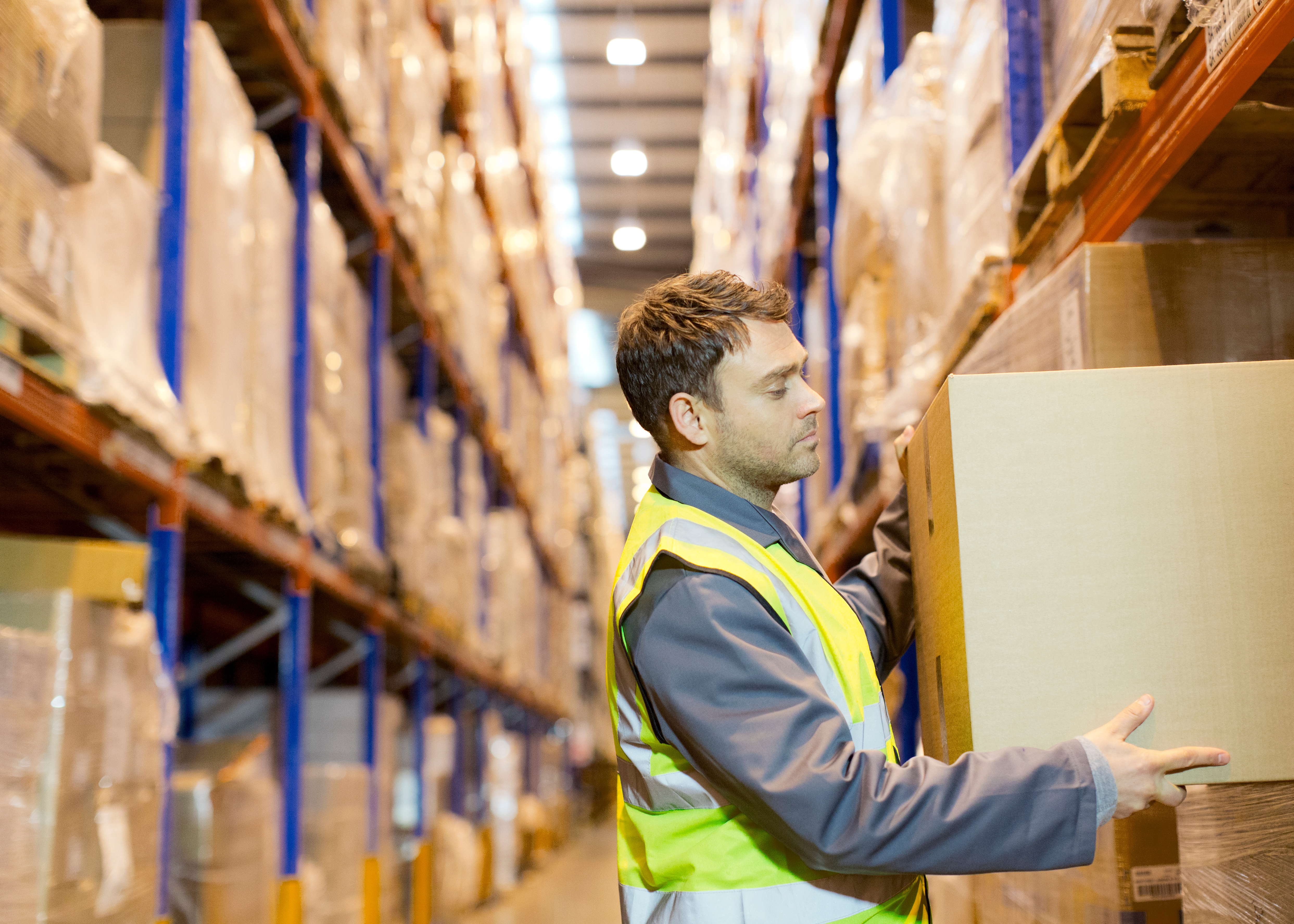
Controlling Worker’s Compensation Costs: Manual Material Handling
By Alliant
Listen to the Audio Version:
Work-related musculoskeletal disorder (WMSD) injuries have a tremendous effect on worker health and workers’ compensation claims. According to the Bureau of Labor Statistics (BLS), musculoskeletal disorders involving the back accounted for almost 40% of all WMSDs. In 2018 the Bureau of Labor Statistics (BLS) reported that musculoskeletal disorders involving the back accounted for 38.5 percent of all work-related musculoskeletal disorders (134,550 back cases out of 349,050 total cases).
The overwhelming majority of WMSD are caused by overexertion or a bodily reaction. The majority of back injuries result from manual material handling (MMH). The good news is businesses can implement control measures and reduce the impact of these types of workers’ compensation claims.
How to Control Exposures
With the understanding that MMH is a main driver of worker injury, what can be done to reduce worker exposures?
The hierarchy of controls for safety solutions follows the graphic below. Businesses can minimize the impact to their workers and productivity by addressing each area of control.
Hierarchy of Controls
PPE and Administrative
The primary personal protective equipment (PPE) solutions for MMH are protective gloves and footwear. Companies focus on administrative controls such as back safety training and job rotation.
- Plan your move
- Size up the load and make sure your path is clear.
- Get assistance as needed.
- Use handles or straps.
- Use a dolly or other materials handling equipment if possible.
- Use a wide, balanced stance with one foot slightly ahead of the other and with your feet flat on the floor.
- Get as close to the load as possible.
- Tighten your stomach muscles as the lift begins.
- Keep your lower back in its normal position with a slight inward curve.
- Pivot and move feet to turn – Do not twist your back.
- Lower the load slowly, maintaining the curve in your lower back.
Job rotation involves decreasing employees’ exposure to manual material handling through a planned-out movement of employees through specific roles and job tasks.
Engineering, Substitution and Elimination
Engineering controls are designs or modifications to equipment, industrial plants, processes or systems that reduce the need for MMH and the associated risks to workers. Ideally, if an employee must perform MMH activities, they are best performed between waist and elbow height.
To limit low and high MMH activities, companies may raise the worker to reduce high force exertions and providing stands or lifts to raise products.
To improve pushing and pulling tasks, companies may improve casters and surface and add powered assists.
Implementation
Businesses should perform an MMH assessment to decide how best to reduce the risk of injury. For any manual handling risk identified, companies should:
1. Ask whether the actual manual handling can be avoided or engineered out of the system.
2. Review whether the exposure can be reduced by rotation.
3. Provide adequate training and PPE to workers.
When selecting the appropriate control measures to minimize the impact of manual material handling, businesses should consider the following:
1. Avoid the need for manual handling.
2. Reduce the load risk by using lighter weights or more stable containers.
3. Reorganize the activity or environment to further reduce the impact on workers.
4. Utilize mechanical lifting aids or equipment.
5. Ensure appropriate rest breaks, job rotation and training are involved.
6. Provide personal protective equipment e.g., gloves, foot protection, non-slip footwear.
How Can Alliant Help?
Alliant Risk Solutions offers creative and powerful strategies with onsite consulting services to help clients effectively respond to the ever-changing circumstances and regulatory landscape. We offer a team of leading specialists to support key loss drivers and exposures.
Our Risk Management Center (RMC) all-inclusive platform creates effective risk mitigation programs for employee safety and compliance. This unique and robust web-based suite of safety and risk management tools provides a risk reduction and safety center for all departments and locations across client organizations, designed to make risk prevention efforts more impactful, cost effective and easier to manage.
Contact Us
Reach out today to request a job safety analysis and ergonomic assessment of your business.
Alliant note and disclaimer: This document is designed to provide general information and guidance. Please note that prior to implementation your legal counsel should review all details or policy information. Alliant Insurance Services does not provide legal advice or legal opinions. If a legal opinion is needed, please seek the services of your own legal advisor or ask Alliant Insurance Services for a referral. This document is provided on an “as is” basis without any warranty of any kind. Alliant Insurance Services disclaims any liability for any loss or damage from reliance on this document.